Understandable production line optimization
As a manufacturing company, the process and planning puzzle is becoming increasingly complex. Consumers are demanding more flexibility, while knowledge-bearing personnel are becoming more costly.
How do you maintain a grip on the production floor?
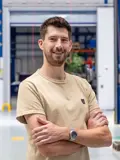
Optimizing production
Production optimization traditionally focuses on large bulk quantities. However, the focus is increasingly shifting to just-in-time delivery of a growing mix to products. Consumers are becoming more demanding with last-minute orders and specific product requirements, which is challenging in the food and process industries.
In addition, it is more difficult to retain knowledge within the manufacturing company as temporary workers increasingly operate production lines. These factors make controlling production lines more challenging. How do you maintain a grip on quality, performance and knowledge assurance? In many manufacturing processes, I regularly encounter the same issues, which I would like to share with you.
Roy Stevelink
Platform Architect
Operators are an important link
The work of a production line operator can be hectic, with many actions and signals that must be executed perfectly to ensure quality and performance. Often, automation solutions forget about operator interaction, leading to crowded screens with buttons and indicators, making focus difficult. During special events, buttons are often pushed randomly.
By developing HMI screens based on operator needs, operators see only relevant information, minimal steps and clear messages. Specialized user experience designers help execute the development process.
This results in:
- Minimization of training time
- Faster detection and resolution of errors
- More calm in the process and more focus on quality
Of course, there are also users with needs for specialized detailed information, such as technical service employees. Because their focus is very different from that of the operator, combining both needs in the same HMI screens is not recommended. It is better to develop separate screens focused on the target audience.
Make use of standards
The market demands ever-increasing product variation. The number of products on a production line is increasing, and changes can occur by the minute. We know this trend as high mix/ low volume batch production. To remain competitive, machine builders must innovate faster and faster and have more and more specialized knowledge. By using the recommended practices in the ISA88 standard, recipes (production steps) and machine configurations (means of production) can be separated. The standards in this batch control architecture prevent failure costs due to unnecessary experimentation. Other benefits include:
- Optimal line utilization through mixed recipes
- Centralized recipes independent of line hardware
- Far-reaching integration of production lines
Complex process environments
Integration of production lines by an experienced system integrator offers significant advantages for manufacturing companies. Because simplifying the system architecture not only leads to an optimally functioning production line. The system can also interact much more easily with other subsystems that consistently use the same standard. After all, multiple individual production lines are part of the overall production process. With the same challenges. How do you keep it understandable and ensure that the overall process continues to function properly? Hierarchical architecture helps tremendously in organizing and structuring complex process environments. By breaking down the process into smaller, more manageable pieces, operators can maintain focus on specific subsystems without losing the overview.
Grip on adjustments through linkages
A third user group is process and planning specialists. They often work off the production floor in systems such as ERP. By linking these to process control, schedules, recipes and properties can be managed centrally. Operators have limited adjustment options, making production fluctuations and unexpected schedules a thing of the past. This improves quality and minimizes waste.
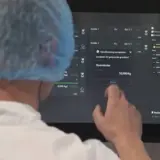
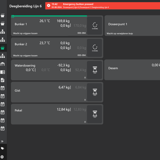

Tracking of raw materials
For full insight into quality and to respond quickly to deviations and audits, balanced accounting is essential. A structured batch control architecture provides a robust basis for accurate recording from silo delivery to (semi-)fabrication. This makes analyses of consumption and origin of raw materials conclusive, even with a large mix of recipes in dynamic and complex process environments.
Optimizing doesn't have to be complex
By viewing optimization as a joint challenge and constantly searching for the root of problems, the finger can quickly be put on the right spot. By making use of standards, solutions arise that excel in simplicity and practical applicability. I myself am a great advocate of comprehensible and well-functioning automation solutions to achieve grip on the production floor. Conforming to the ISA88 standard, I design and optimize our RIMOTE Production and Process platform on a daily basis with all kinds of building blocks to be able to reuse functionality modularly and flexibly in different industrial process environments. In doing so, we ensure continuous innovation for our customers!
Recognizable challenges from daily practice? We would like to see how we can unburden you with understandable production line optimizations. Please contact us for an informal discussion!
Be convinced
by the power
from RIWO
Contact us for more information.