Worry-free automation
Industries worldwide strive for efficiency and reliability. The idea of worry-free automation captures the imagination of many companies: systems that work together, without human intervention, without errors. But how do you achieve this ideal state?
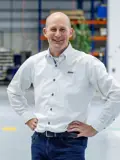
Carefree production
Manufacturing companies want to be able to produce worry-free and independently for many years. Industrial automation and control offers all kinds of interesting possibilities for achieving this goal. The market is calling more and more for automated production machines and systems with controls of ever-increasing autonomy. OEM Machine builders regularly struggle with this trend. In this Tech Talk, we dive into the world of industrial automation and I share some essential tips for a worry-free implementation.
Wim Spit
Director
Use of A manufactured products
Reliable and robust hardware that can withstand the industrial environment is essential for worry-free automation. Equipment must withstand extreme temperatures, humidity, dust and vibration to ensure continuous and error-free operation under harsh conditions. Because of stringent quality controls, certifications and high manufacturing standards, the use of A-grade fabrications reduces the likelihood of defects and failures. As a result, availability is better assured. Leading manufacturers also offer well-supported software solutions to achieve reliability and continuity of production processes. In short, A-fabricates offer benefits through better overall performance of control sets over the entire life cycle.
Interoperability
Integration and compatibility of controls in the industrial environment is essential for worry-free automation. All components must work together smoothly, from sensors and actuators to PLCs and process controls, regardless of manufacturer. This requires the use of standardized protocols and interfaces to avoid communication problems and facilitate system expansions. A well-integrated system can exchange data quickly and reliably, leading to higher levels of safety, improved performance and reduced downtime. It is precisely by using standards that the wheel does not have to be reinvented each time and can focus on unique functionality. As a result, major advantages are gained in terms of development time, knowledge sharing and serviceability, among others.
Regular maintenance and updates
Maintenance and updates of industrial controls are critical to ensure the reliability and efficiency of automated systems. Regular preventive maintenance helps minimize wear and unexpected failures, which extends the life of hardware. Software updates are equally important because they plug security holes, fix bugs and add new functionality. By implementing a structured maintenance plan, using spare parts and updating software regularly, manufacturing companies can produce worry-free.
Workshops and trainings
To properly prepare employees to work with controls in the industrial environment, workshops are valuable for the operation and maintenance of automated systems. This improves staff skills, reduces the likelihood of human error and increases operational efficiency. Training ensures that employees can respond appropriately to malfunctions and make optimizations on their own. Regular workshops also encourage a culture of continuous improvement. And, of course, this doesn't just apply to users of systems. Workshops and training also contribute to adequate service delivery by well-trained service employees.
Monitoring and notifications
Monitoring and reporting incidents to industrial systems provides insight into system performance. By continuously collecting and analyzing data, companies can identify operational trends, detect potential problems early and take proactive action to minimize downtime. Automated notifications ensure that relevant stakeholders are immediately notified of critical events, enabling quick decision-making and maximizing system uptime.
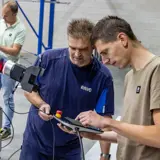
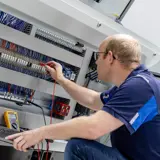
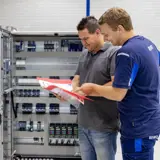
Systems integrator
Find a systems integrator where all control disciplines for industrial automation and control can be found under one roof. It is nice to have only one point of contact for increasingly complex automation issues. By combining expertise, such an integrator can deliver customized solutions that meet the specific automation need. This ensures seamless integration of different systems and optimizes operational efficiency. In addition to benefiting from technical expertise, a coordinated approach to project management also results in faster implementation times and better support during the systems life cycle.
No utopia
So worry-free automation in the industrial sector is certainly not a pipe dream. Our staff helps OEM machine builders with the right approach so that manufacturing companies can benefit from increased productivity, consistent quality, cost savings and improved safety. By investing in reliable automation systems, regular updates and well-trained employees, manufacturing companies can optimize their automation processes and produce worry-free.
Has your company already taken steps toward worry-free automation? Are you looking for more information or advice? Contact us for a no-obligation consultation!
Be convinced
by the power
from RIWO
Contact us for more information.