Greenhouse robot
Agri - Systems integration - Machine control
Spraying, pouring, fighting, inserting, taking out and widening of planting material in greenhouse complexes.
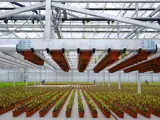
Background
Achterbosch Mechanical Engineering offers a wide range of technical services. From welding to machining and bending using modern CNC machines to developing and manufacturing complete machines. We have been working together for many years to develop total solutions for the internal logistics of pot and tray plants in combination with sprinkling, pouring or control. Combining our proven concepts with customer-specific customization creates a cost-efficient total solution for growers. Together with Achterbosch we developed, among other things, the greenhouse robot.
The robot is designed as a trolley that rides on rails installed at the top of a horticultural greenhouse. Thanks to its multifunctional nature, a single machine can be used to solve various functionalities. Moreover, it is easy to start and expand functionality. The high degree of robustness makes this rail car suitable for the demanding environmental conditions demanded in the horticultural industry. Its modern controls make this robot suitable for working closely with other machines to fully automate the internal logistics of horticultural companies.
Challenge
Many crops are grown in various sizes of pots and trays. This range of planting material is grown in huge numbers and must be moved within greenhouse complexes. In addition to supplying, removing and widening crops, there is a need for sprinkling, watering or pest control during cultivation. The robot offers a multifunctional solution for all these needs. Environmental conditions such as temperature differences, humidity and varying greenhouse configurations must be taken into account. Moreover, the system must be custom configurable for all these situations. In addition to performing automatic tasks, the solution must also be easy to use manually and possibly in combination with a central process controller.
Solution
The base of the robot is a solid frame with that moves over steel rails at height over the crop. A scissor mechanism can be used to attach implements, such as a smart handle to automatically move a block of plants in and out of the canopy or to widen it. It is also used for irrigation, watering or pest control.
The machine is distinguished by its modern controls. For example, the touchscreen can be operated remotely via a smartphone, it positions the trolley accurately, communicates wirelessly with the environment such as with hoisting or transport trolleys, and works optimally with the central process control when complex business processes are required. A comprehensive configuration matrix allows the machine to be optimally tailored to company-specific situations and required functionality.
The standard version is suitable for 8m hoods and can be customized customer-specifically. For reliable positioning, RFID transponders are used so that slip and expansion of rails are compensated.
Be convinced
by the power
from RIWO
Contact us for more information.