Metal recycling
Industry - System integration - Machine control
Separating non-ferrous with advanced sensing and robotics.
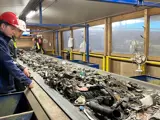
Background
Recycling metals helps conserve natural resources such as ores and minerals. Using recycled metals instead of new ones reduces pressure on natural resources. Recycling metals also significantly reduces the energy required to smelt and process ore, which helps save energy and reduces greenhouse gas emissions.
With the global scarcity of metals such as copper, brass, bronze and aluminum, the need to reuse them from complex products such as cell phones, cars or washing machines is increasing.
Riwald Recycling recycles many hundreds of thousands of tonnages of waste materials every year, ranging from demolition waste, industrial high-value residues, to railcars and aircraft. These materials are then recycled into more than 150 types of sustainable raw materials. The company continuously invests in a green future and uses a unique high-tech granulator in combination with attached separation installations for maximum recovery efficiency with current techniques.
Challenge
In various sub-processes and process steps, industrial waste streams are machine reduced, sorted and separated into end products such as ferrous (steel, cast iron, stainless steel), non-ferrous (aluminum, copper, lead, zinc, bronze, brass), plastic and dirt. Various technologies are used in this process.
At the end of the machine separation process, a residual stream of non-ferrous remains, which for now can only be sorted by human hands. The goal of this innovation project is to reduce the required hand-picking capacity and largely automate this process with advanced detection methods and robotics. The difficulty is that current techniques isolated cannot unambiguously select this residual stream, so multiple techniques and measurements may need to be taken together to reliably and robustly classify the parts in this residual stream.
Solution
The scope of this innovation project is a challenging issue where the complementary and experienced organizations Riwald, RIWO and TValley are working together intensively for 3 years. In order to continue to produce in line with the 2030 & 2050 goals of the central government, a machine is being developed that can automatically and cleanly separate residual streams using advanced sensors, software and robotics.
The premise of the project is that the remaining material stream will be singulated. Feathering allows multiple properties of a material to be sampled. The real game changers in terms of innovation within the project are sensor fusion and AI, key building blocks within our RIBOTIC Perception platform. Affordable sensor techniques are cleverly combined, obtaining information about the metal part to be inspected with a greater degree of certainty. Should the accuracy of the system prove suboptimal, it can be improved by incrementally adding more (costly) sensor technologies to the sensor fusion model.
Multiple robots are then controlled using our RIBOTIC Manipulation platform to singulate the erratically shaped metal parts.
Be convinced
by the power
from RIWO
Contact us for more information.