Triomatic feeding robot
Agri - Systems integration - Machine control
An automatic self-propelled feeding robot for accurate feeding of cattle.
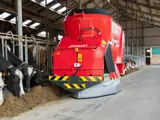
Background
Trioliet is engaged in the development, production and sale of machines and systems for feeding cattle on cattle farms. It is proven that more frequent feeding results in higher feed intake, higher milk production, better health and higher fertility of the herd. To be able to feed more often, modern livestock farmers are increasingly choosing an automated feeding system.
Together with Trioliet, we developed the automatic feeding system Triomatic, where simplicity is the strength. Due to scaling up and professionalization, the need for automated feeding systems is increasing and customer expectations are changing. The feeding robot, as part of the total feeding system, must be made suitable for more complex business situations and the installation time must be reduced. Therefore, the desire arose to have the robot run on wheels and batteries instead of a heavy suspension construction or power rail systems like previous generations
Challenge
To achieve an effective feed intake rate for cattle, the volume of ration feed required to be carried by the feed robot is considerable. Moreover, to mix such volumes, a hefty battery system is required, leading to a substantial increase in cost. Also, the geometry of the robot combined with its weight places high demands on the controls. Another challenge is the simplicity of installation processes, which must be able to be carried out in a short time frame by employees without in-depth control knowledge.
Solution
Using RFID transponders and wire guidance creates a robust form of navigation. Farm infrastructure often covers multiple buildings that must be reliably reached in all weather and soil conditions. By using the Ribotic navigation antenna, the cost can be dramatically reduced compared to previous generations of this feeding robot.
The feeding robot rides on wheels and is equipped with a high-energy-density battery pack for driving, dispensing and feeding. In the feed kitchen, the feed robot docks on a power rail to charge the batteries and to drive and mix on mains power in the feed kitchen. The mixing process requires a lot of energy; seamlessly switching between batteries and mains power avoids an excessive battery pack.
For navigation, the Triomatic WB robot uses an antenna that follows an induction wire or transponders in the floor. This makes it possible to drive without the need for a rail, even between different stalls in a yard. Thanks to the Rimote integration, the system can be remotely operated, serviced and users are notified when needed, for example reporting an empty feed store.
Be convinced
by the power
from RIWO
Contact us for more information.