Wrapping machine
Energy - Systems integration - Machine control
A prototype machine to manufacture heat exchangers for window frames.
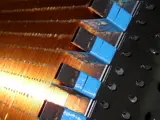
Background
Manufacturing frame heat exchangers where heat transfer is achieved with thin copper wires (air-to-air transfer). Breathing windows in the facade can provide the desired ventilation and a healthy indoor environment with minimum energy loss.
The machine produces semi-finished products that are assembled into finished products in a subsequent process. It involves two fans generating opposing airflows with a so-called "thin-wire heat exchanger" between them.
Challenge
The quality of indoor air in Dutch homes is often not good enough. This certainly applies to homes that have been post-insulated in the past. In homes with mechanical ventilation, the ventilation system is often so polluted that the air is also no longer adequately refreshed.
That can be solved with a thin-wire heat exchanger with 15 kilometers of 0.1-mm-thick copper wire applied in 28 layers. The wires must be applied at very precise intervals and the adhesive package must be completely airtight.
Solution
The final product is composed of a combination of plastic and copper wires that creates an exchanger with extremely high efficiency. The exchangers are built into window frames to allow ventilation but to prevent drafts. The machine spools the copper wires on a large drum to then stretch a plastic layer between them, these plastic wires are glued to the copper package. Operation and tolerances are secured by the use of servo technology. At the end of the machine cycle, a mat is created which forms the basis for the heat exchanger. The mats are provided with plastic caps in a mold to fit the recess in the frame.
Be convinced
by the power
from RIWO
Contact us for more information.